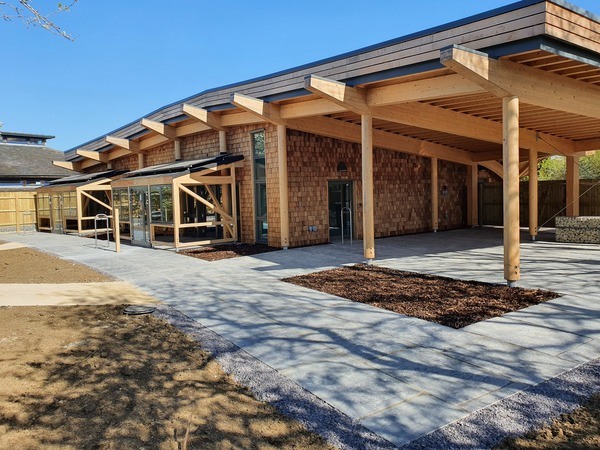
THE PROJECT
Earth Lab sits at the heart of the Earth Trust Centre, providing a
stimulating, interactive and inspirational education space. Designed in sympathy with the surrounding landscape, it compliments the natural
beauty of a stunning site and provides a seamless flow between indoor to
outdoor learning areas.
The vision was for the classrooms to be alive with learning, providing
hands-on immersive experiences that fully engage learners
with the environment around them, from natural sciences, history and ecosystems to STEM.
Earth Lab has received multiple awards and commendations,
including the Most Innovative and Sustainable Initiative of the Year at the
2021 OxPropFest Awards and in 2022, winner of the the Best Sustainability
category in the SPRA awards for the building’s curved structured green roof.
£1.5M
CONTRACT VALUE
59 WEEKS
CONTRACT DURATION
Customer
Earth Trust
Architect
White Design
Associates
Quantity Surveyor
Baqus Group
SUSTAINABLE CONSTRUCTION
Earth Trust's careful approach to managing green spaces was embraced throughout the design and construction of Earth Lab.
Encouraging sustainable behaviours, selecting the best materials
and partners to realise the design and reducing the impact of construction activities and waste, were all at the forefront of our thinking.
Locally available sustainable materials, containing less embodied carbon, were explored whilst also considering the the long term
performance of the building.
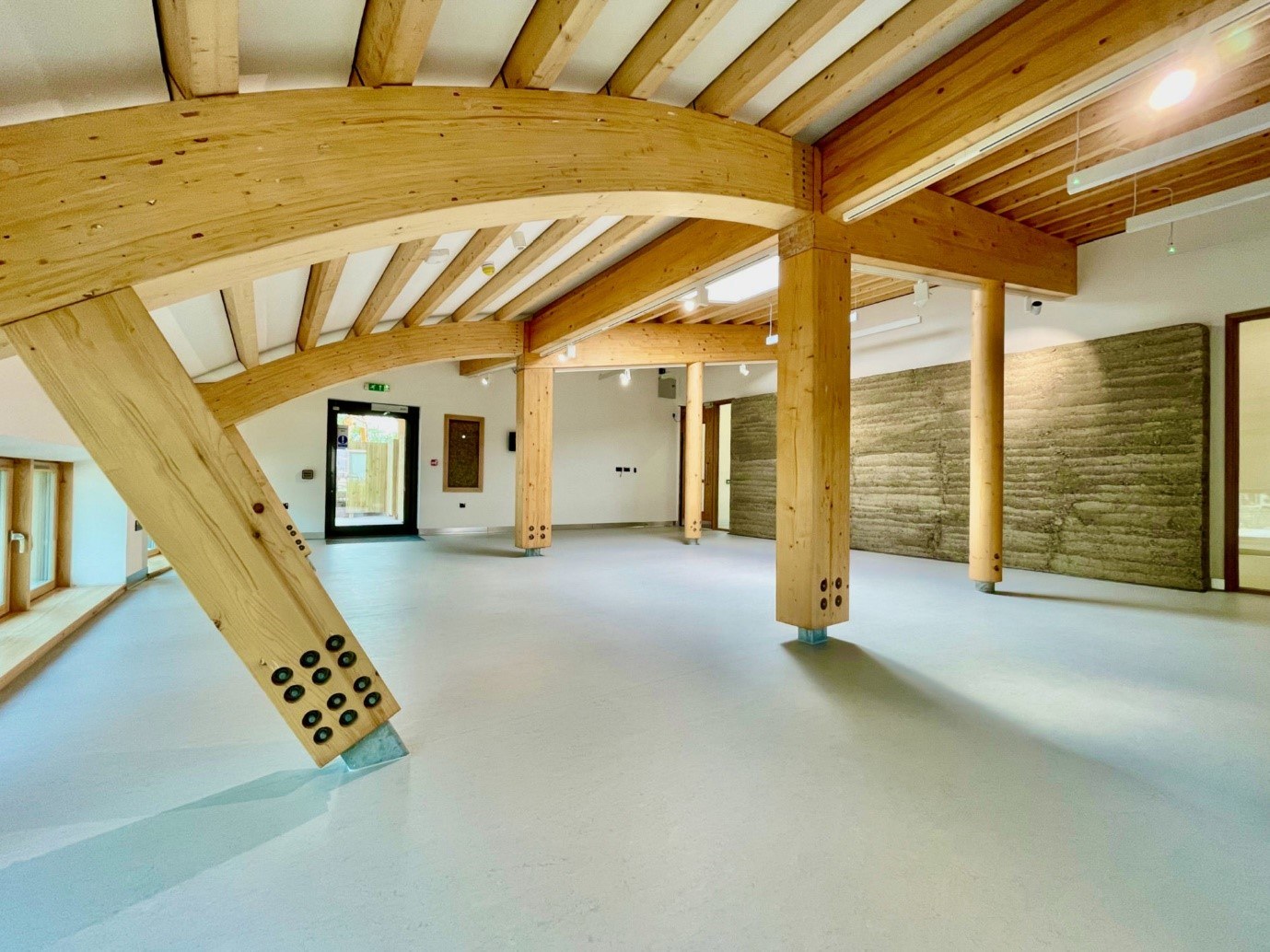
Glulam beams
As a natural alternative to steel or bricks, glulam beams were used to form the structural elements of the
walls and roof. The energy used to fabricate a glulam beam is 5-6 times less than a steel or concrete beam of the same mass and length.
All of
the straight glulam beams have been made by a German glulam manufacturing firm,
specialising in the mass production of standard spruce glulam. Produced using highly energy efficient machinery and manufacturing systems, going a long way to offsetting the carbon emissions of the haulage. The
curved beams were manufactured by UK specialist Buckland Timber, based in
Devon. The raw glulam materials are machined by hand, before fitting metalwork
as necessary and sending them to site.
All of
the timber used to manufacture the glulam beams was sustainably
grown PEFC certified spruce of Scandinavian origin.
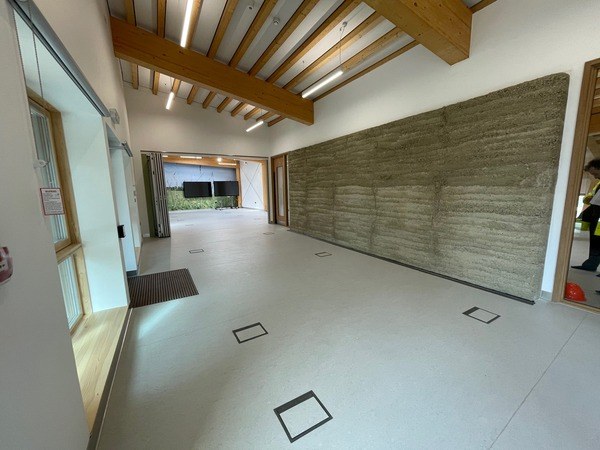
Rammed earth wall
One of the prominent features of the project is the rammed
earth wall.
Rammed earth walls act as a
natural heat and humidity regulator, which is extremely useful for spaces with
significant flows of people. Advice was sought from Rowland Keble, a rammed wall specialist who was significantly involved in the Eden
Project in Cornwall.
The materials for the wall have been carefully selected
from spoil arising from the reduced level and foundation excavations on the
site, mixed with soil from archaeological excavations at Little Wittenham.
A small
demonstration section was erected outside the Earth Trust Centre in order
to test the suitability of the local materials. This section remains in place
to give visitors an insight into the construction process.
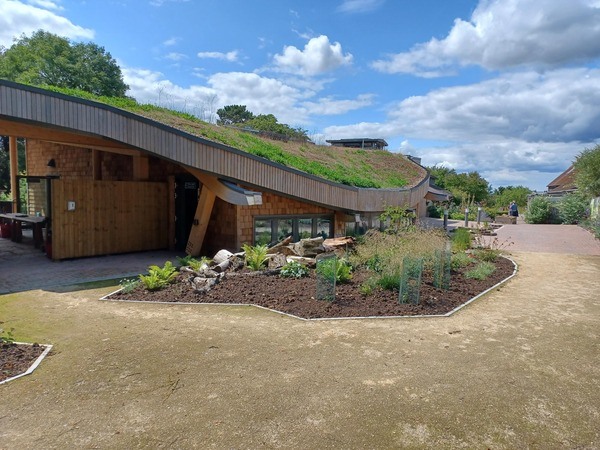
Wildflower roof
The roof
of the Earth Lab is a true green roof with the ability to support wildflowers.
It offers multiple benefits including habitat creation, increasing
biodiversity, water filtration and reuse through an underground attenuation system, and carbon capture.
Species are
reflective of the wildflowers native to the area, and were introduced through a
combination of plug planting and seeds.
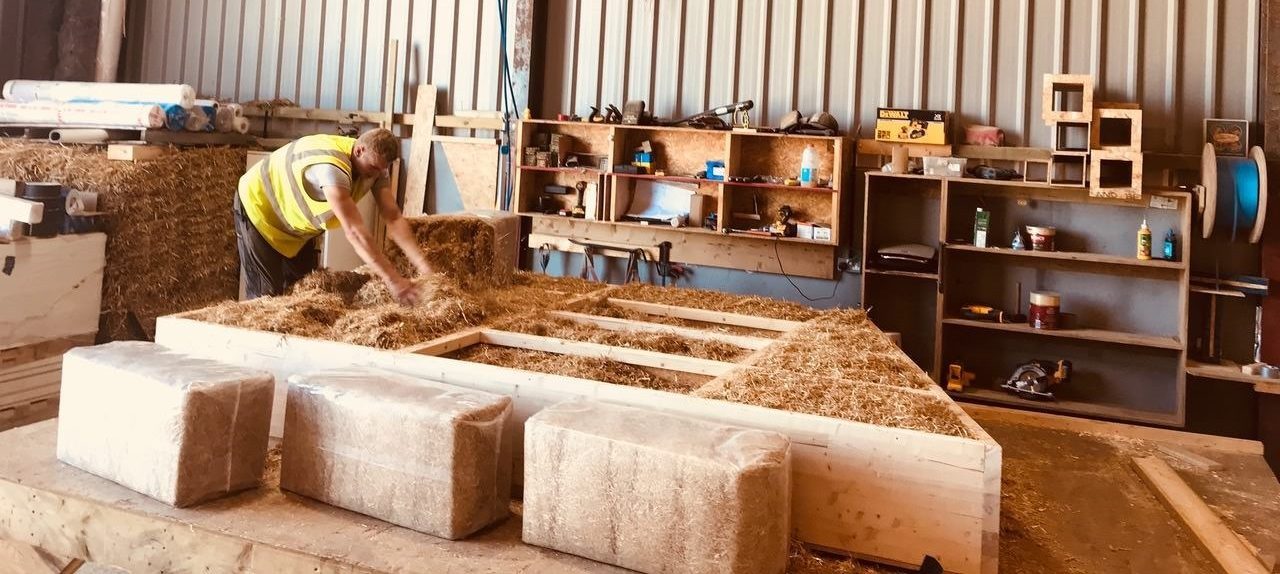
Straw insulation
Prefabricated cells, containing shredded and compacted straw, were chosen for insulation. The cells are constructed from a timber frame, insulated with straw and clad to the faces with plywood. Being prefabricated, journeys to site were also reduced.
The ModCell frames at Earth Lab were constructed using FSC or PEFC timber sourced in the UK.
(Images: Agile Property & Homes)
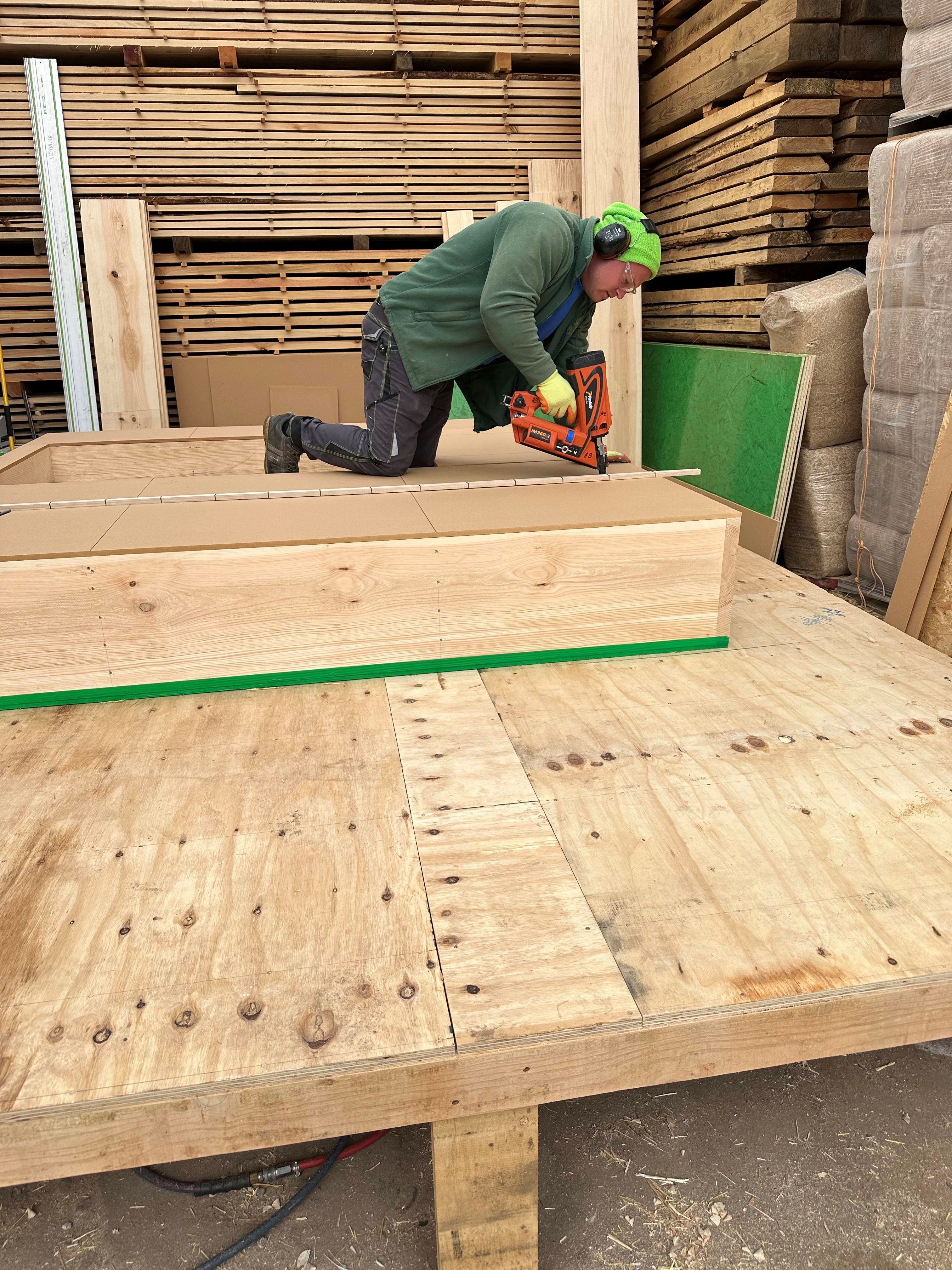
Waste generated during the manufacturing process is reused as animal bedding, or turned into biomass fuel along with the timber off cuts, and used in the manufacturer’s biomass boiler.
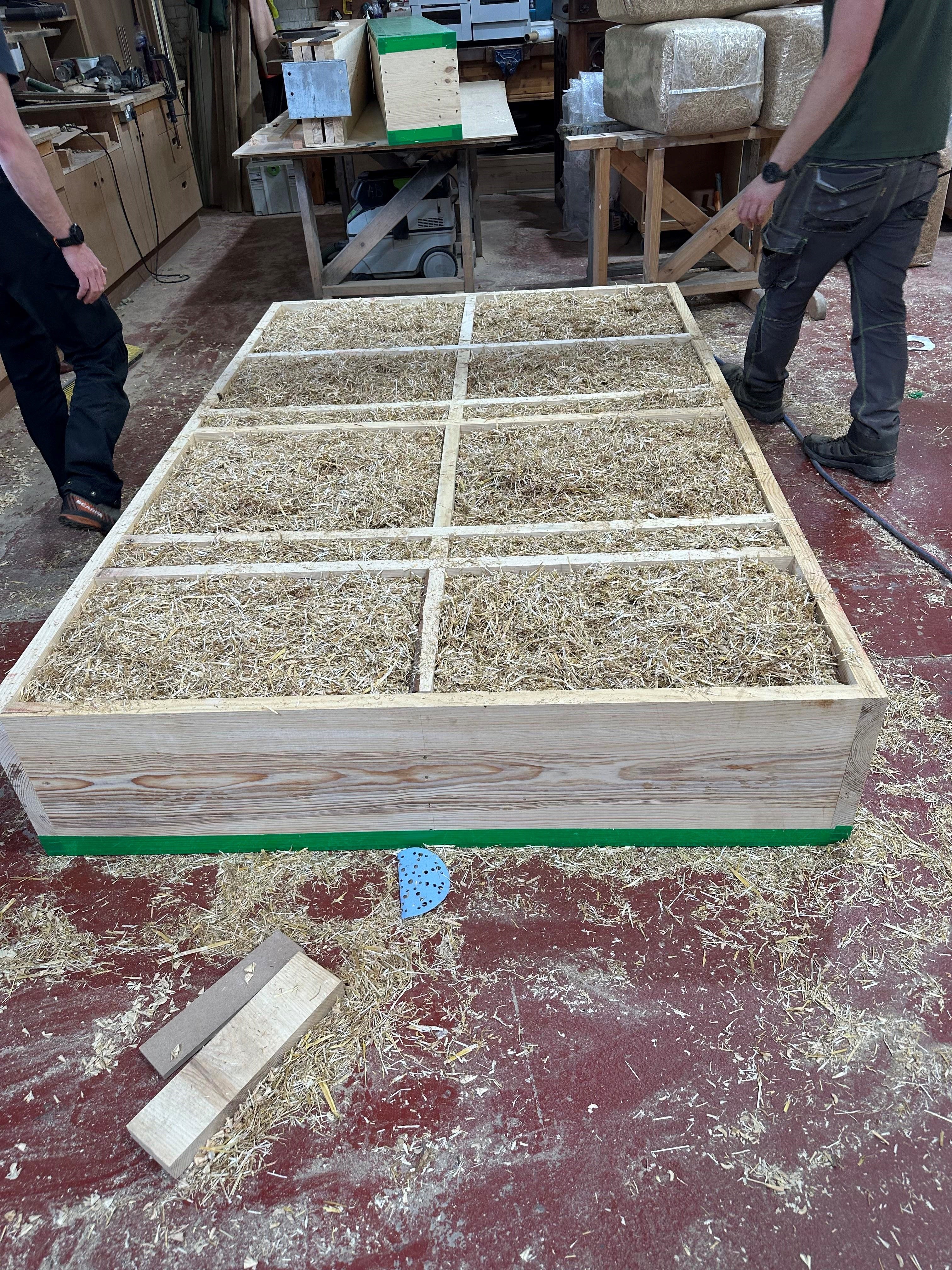
ModCell deliveries were made on two vehicles and lifted into final position to reduce the labour force on site along with the noise and dust typically generated from traditional construction methods.
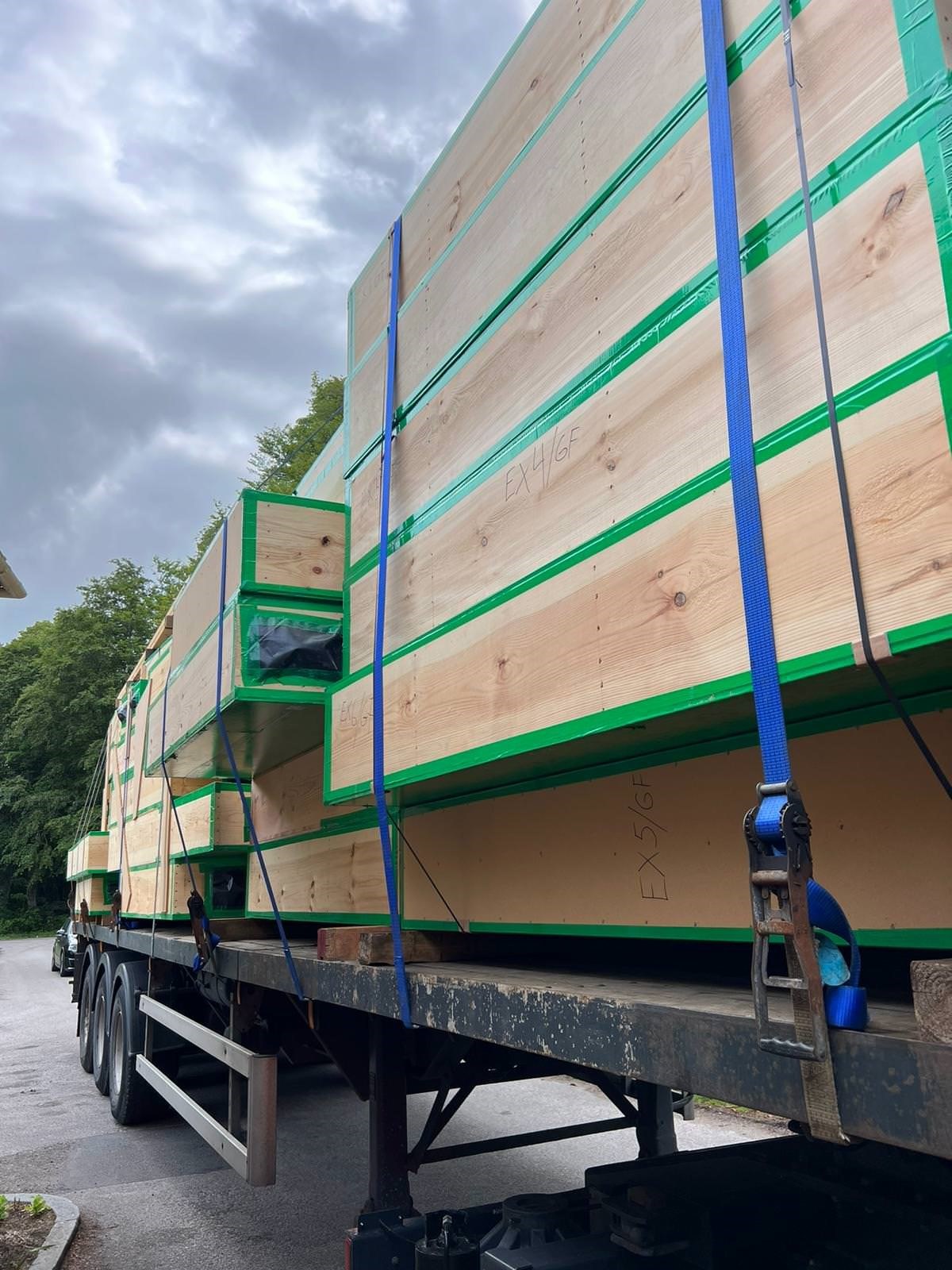